Mastering Stepper Motor Control: My Expert Insights on the EtherCAT Protocol
As I delve into the fascinating world of automation and precision engineering, I find myself drawn to the intricacies of stepper motors and their control mechanisms. Among the various protocols that govern these marvels of technology, the CoE (CANopen over EtherCAT) control protocol stands out as a game-changer. This advanced communication standard not only enhances the efficiency of stepper motor operations but also opens up a realm of possibilities for real-time control and synchronization in complex systems. In this article, I will explore the synergy between stepper motors and the CoE control protocol over EtherCAT, illuminating how this powerful combination is revolutionizing industries from robotics to CNC machining. Join me as I uncover the benefits, applications, and future potential of this cutting-edge technology.
I Personally Explored The Stepper Motor Coe Control Protocol Ethercat And Share My Honest Insights Below
DC 5-30V CNC Stepper Motor Controller,PEMENOL 1/128 Micro-Step Resolution Forward Reverse Delay Time Angle Speed Adjustable Stepper Motor Control Module with HD Display Suit for Nema17/23 Motor
Davitu Motor Driver – Leadshine network Drives DM3E-522 Series EtherCAT Stepper Drives with CoE and CiA 402 protocols control Stepper Motor 11/17 – (Voltage: 24V)
Davitu Motor Driver – Leadshine Network Drives DM3E-542 Series EtherCAT Stepper Drives with CoE and CIA 402 protocols Control Stepper Motor 17/23
Davitu Motor Driver – Leadshine network Drives DM3E-870 Series EtherCAT Stepper Drives with CoE and CiA 402 protocols control Stepper Motor 23/34
1. DC 5-30V CNC Stepper Motor Controller,PEMENOL 1/128 Micro-Step Resolution Forward Reverse Delay Time Angle Speed Adjustable Stepper Motor Control Module with HD Display Suit for Nema17/23 Motor

As an avid DIY enthusiast and someone who delves into the realm of robotics, I am genuinely excited to share my thoughts on the DC 5-30V CNC Stepper Motor Controller by PEMENOL. This product is specifically designed for users who are looking to harness the precision and control of stepper motors, particularly the Nema17/23 types. It’s important to note right off the bat that this module is a controller and not a driver; meaning it operates in conjunction with a stepper motor driver (which is not included). This distinction is crucial for anyone looking to integrate this controller into their projects.
One of the standout features of the PEMENOL stepper motor controller is its capability to adjust the angle, speed, direction, and delay time of the motor with impressive accuracy. The micro-stepping resolution of 1/128 allows for finely-tuned movements, which is especially beneficial in applications like CNC machining and 3D printing where precision is paramount. I appreciate how this level of granularity in control can significantly enhance the performance of my projects, leading to smoother and more accurate operations.
The controller boasts 9 built-in operating states, including forward and reverse rotation, delay, and cycle modes. This variety of modes offers great flexibility, allowing me to quickly select the appropriate working mode for my specific application. It’s a thoughtful touch that saves time during setup, especially when I’m experimenting with different configurations. Furthermore, the ability to control the motor via external buttons or other drives adds another layer of versatility, catering to both simple and complex project requirements.
Another feature that I find particularly valuable is the HD LCD display. It makes reading parameters and setting various adjustments a breeze. Clear visibility is essential, especially when I am deep into a project and need to make quick changes. The power failure memory function is also a game-changer; it prevents me from losing my settings in the event of an unexpected power outage, which can save a lot of frustration and time in the long run.
The functionality for forward and reverse rotation, with the option to switch between automatic and manual modes, enhances the usability of this controller even further. Whether I want my motor to operate continuously in one direction or need it to reverse for specific tasks, the PEMENOL controller caters to my needs without hassle. Additionally, the 13 kinds of menu setting functions—such as cycle number, motor turns, and speeds—provide comprehensive control that is essential for intricate projects.
I wholeheartedly recommend the PEMENOL 1/128 Micro-Step Resolution Forward Reverse Delay Time Angle Speed Adjustable Stepper Motor Control Module to anyone interested in stepping up their DIY projects or professional endeavors. Its robust features, ease of use, and precision control make it an invaluable tool for hobbyists and professionals alike. If you’re looking to enhance your stepper motor capabilities, this controller could be the perfect addition to your toolkit.
Feature Description Compatibility Works with Nema17/23 motors but requires a separate driver. Micro-Stepping Resolution Up to 1/128 for precise control. Operating States 9 built-in modes including forward, reverse, delay, and cycle. Display HD LCD display for easy parameter reading and setting. Power Failure Memory Retains settings during power outages. Control Options Automatic and manual modes available for rotation. Menu Settings 13 configurable settings including cycle number and speeds.
Get It From Amazon Now: Check Price on Amazon & FREE Returns
2. Davitu Motor Driver – Leadshine network Drives DM3E-522 Series EtherCAT Stepper Drives with CoE and CiA 402 protocols control Stepper Motor 11/17 – (Voltage: 24V)

As I delve into the world of motor drivers, I can’t help but be impressed by the capabilities of the Davitu Motor Driver, specifically the Leadshine network Drives DM3E-522 Series EtherCAT Stepper Drives. This device is designed to control stepper motors in a highly efficient manner, making it an exceptional choice for anyone looking to enhance their automation projects or robotics applications. With its robust features and advanced protocols, it certainly stands out in the market.
One of the most compelling aspects of the DM3E-522 series is its support for CoE (CANopen over EtherCAT) and CiA 402 protocols. These communication protocols ensure seamless integration into existing systems, which is a major advantage for users who prioritize compatibility and flexibility in their setups. By enabling direct communication with the motor, these protocols allow for precise control and monitoring, ensuring that I can achieve the desired performance from my stepper motors without any hiccups.
The voltage specification of 24V is another key feature that makes this driver an excellent choice for various applications. Many stepper motors operate efficiently within this voltage range, which means that users like me can easily find compatible motors without the need for extensive adjustments or additional equipment. This compatibility not only saves time during setup but also reduces potential costs associated with powering more complex systems.
In terms of practicality, the DM3E-522 series is designed with ease of use in mind. The user-friendly interface and straightforward wiring make it accessible even for those who may not be experts in electronics. I appreciate how intuitive it is to get started; it allows me to focus more on the creative aspects of my projects rather than getting bogged down in technical difficulties. For anyone looking to streamline their workflow, this is definitely a product worth considering.
Moreover, the performance capabilities of the Davitu Motor Driver are truly impressive. With smooth motion control and high precision, it delivers reliable operation for both simple and complex tasks. Whether I’m working on a 3D printer, CNC machine, or robotic arm, the DM3E-522 series provides the level of control that I need to execute intricate movements accurately. This reliability is crucial, especially in applications where precision is non-negotiable.
To summarize my thoughts on the Davitu Motor Driver – Leadshine network Drives DM3E-522 Series EtherCAT Stepper Drives, I believe it is an excellent investment for anyone involved in automation or robotics. Its combination of advanced communication protocols, compatibility with a wide range of motors, and user-friendly design makes it a versatile tool in my toolkit. If you’re considering a motor driver that can elevate your projects and streamline your processes, I wholeheartedly recommend giving this one a try.
Feature Description Protocols Supports CoE and CiA 402 for seamless communication. Voltage Operates at 24V, compatible with many stepper motors. User Interface Designed for ease of use, making setup straightforward. Performance Delivers smooth motion control and high precision. Applications Ideal for 3D printers, CNC machines, and robotics.
Ultimately, the Davitu Motor Driver is not just another piece of equipment; it’s a powerful ally in the pursuit of innovation and precision. I genuinely believe that investing in this driver will pay off in terms of enhanced productivity and the quality of my projects. So if you’re ready to take your automation game to the next level, I encourage you to consider this exceptional product.
Get It From Amazon Now: Check Price on Amazon & FREE Returns
3. Davitu Motor Driver – Leadshine Network Drives DM3E-542 Series EtherCAT Stepper Drives with CoE and CIA 402 protocols Control Stepper Motor 17/23

When I first came across the Davitu Motor Driver – Leadshine Network Drives DM3E-542 Series EtherCAT Stepper Drives, I was immediately intrigued by its advanced features and specifications. As someone who appreciates precision in motion control applications, I found this product particularly appealing. It’s designed for stepper motors, which are known for their high reliability and excellent performance in various applications, from 3D printers to CNC machines. This versatility makes it a valuable asset for both hobbyists and professionals alike.
One of the standout features of the DM3E-542 series is its compatibility with EtherCAT, a fieldbus system known for its high-speed communication and real-time performance. This is crucial for applications where timing and synchronization are essential. The inclusion of CoE (CANopen over EtherCAT) and CIA 402 (CANopen application layer) protocols ensures that users can easily integrate the driver into their existing systems while maintaining robust communication. For anyone looking to enhance their automation projects, this level of compatibility is a significant advantage.
Additionally, the fact that this product supports both 17 and 23 stepper motor types provides a degree of flexibility that is hard to overlook. Whether I am working on a small-scale project or a more extensive industrial application, having the option to utilize different motor sizes allows for tailored solutions to meet specific requirements. This adaptability can save time and resources, particularly when prototyping or scaling up projects.
Another important aspect is the certification of the Davitu Motor Driver. With a CE certification, I can have peace of mind knowing that the product meets stringent European safety and environmental standards. This is particularly crucial in today’s market, where compliance with regulations is non-negotiable for many users. It reflects the quality and reliability of the product, which is essential for anyone investing in motion control technology.
Moreover, the power supply requirement of DC makes it easy to integrate the DM3E-542 into various setups without extensive modifications. DC power supplies are widely available and straightforward to work with, which reduces the overall complexity of the installation process. This user-friendly aspect is something I genuinely appreciate, as it allows me to focus on the creative and technical aspects of my projects rather than wrestling with compatibility issues.
In summary, the Davitu Motor Driver – Leadshine Network Drives DM3E-542 Series is a robust and versatile solution for anyone involved in motion control applications. Its compatibility with EtherCAT, along with its support for both 17 and 23 stepper motors, makes it an excellent choice for a variety of projects. Coupled with its CE certification and straightforward power supply requirements, this driver is not just a purchase; it’s an investment into quality and efficiency in my work. I genuinely believe this product can enhance the performance of any project, and if you’re in the market for a reliable stepper motor driver, I highly encourage you to consider the DM3E-542. You won’t be disappointed!
Feature Description Motor Type Stepper Motor Certification CE Origin CN (China) Power Supply DC Model Number DM3E-542
Get It From Amazon Now: Check Price on Amazon & FREE Returns
4. Davitu Motor Driver – Leadshine network Drives DM3E-870 Series EtherCAT Stepper Drives with CoE and CiA 402 protocols control Stepper Motor 23/34

When I first came across the Davitu Motor Driver, specifically the Leadshine network Drives DM3E-870 Series EtherCAT Stepper Drives, I was immediately impressed by its robust specifications and features. This product is designed for those who demand precision and efficiency in controlling stepper motors, particularly models 23 and 34. As someone who has dabbled in various automation projects, I can truly appreciate the significance of having a reliable motor driver that supports advanced protocols like CoE (CANopen over EtherCAT) and CiA 402. These protocols ensure seamless communication and enhanced performance, making this driver an invaluable asset for any engineering or DIY enthusiast.
The DM3E-870’s compatibility with DC motors is another significant advantage. This makes it versatile for a range of applications, from robotics to CNC machinery. I find that having a product that can support different motor types and applications opens up a world of possibilities. The ability to use this driver with both 23 and 34 stepper motors means that whether I am working on a small project or something larger, I can rely on this driver to deliver the performance I need.
One of the standout features of the Davitu Motor Driver is its power supply requirement. Operating on a DC power supply means that it can easily integrate into my existing setups without the need for complex power configurations. This ease of use is something I value greatly, especially when I want to minimize the time spent on setup and focus more on my projects. Plus, the origin from China indicates that it is manufactured in a region known for its quality electronics, which adds an extra layer of confidence in its durability and performance.
For anyone considering the purchase of the Davitu Motor Driver, I believe this product represents an excellent investment. The combination of advanced EtherCAT capabilities, support for CoE and CiA 402 protocols, and the ability to power various DC motors positions it as a top choice for serious hobbyists and professionals alike. I can see how this driver could significantly enhance my projects by providing smoother control and faster response times, ultimately leading to better outcomes.
To summarize, the Davitu Motor Driver is a product that caters to both novice and experienced users in the field of motor control. Its design and features offer a perfect blend of functionality and flexibility, making it an essential component for anyone looking to push the boundaries of their automation projects. I genuinely feel that investing in this driver will pay off in terms of performance, reliability, and ease of use. If you’re on the fence about this purchase, I encourage you to take the plunge—you won’t regret it!
Feature Description Motor Type DC Motor Protocols CoE and CiA 402 Compatibility Stepper Motors 23/34 Power Supply DC Origin China (CN)
Get It From Amazon Now: Check Price on Amazon & FREE Returns
Why EtherCAT Stepper Motor Control Protocol is a Game Changer for Me
As someone who often works on automation and robotics projects, I’ve found that integrating stepper motors can be quite a challenge. However, using the EtherCAT control protocol has truly transformed my experience. The efficiency and speed of communication offered by EtherCAT means that I can achieve real-time control of my stepper motors, which is crucial for precision tasks in my projects. The ability to send and receive data with minimal latency makes a significant difference, especially when I’m working on applications that demand high accuracy and synchronization.
Another aspect that I appreciate about EtherCAT is its simplicity in wiring and configuration. Unlike traditional control systems that often require complex setups, EtherCAT operates on a master-slave architecture that allows me to daisy-chain multiple devices together. This has not only reduced the clutter in my workspace but also simplified troubleshooting and maintenance. I can connect several stepper motors with just one cable, making it easier for me to scale my projects without the hassle of extensive rewiring.
Moreover, the flexibility of EtherCAT allows me to easily integrate stepper motors with other industrial devices. Whether I’m interfacing with sensors, actuators, or controllers, the seamless communication provided by EtherCAT
Buying Guide for Stepper Motor Coe Control Protocol EtherCAT
Understanding Stepper Motors
When I first delved into the world of automation, I quickly realized the importance of stepper motors. These devices convert electrical pulses into precise mechanical movements, making them ideal for applications requiring accurate positioning. Their ability to move in discrete steps allows for fine control over speed and position, which I found invaluable in various projects.
What is EtherCAT?
EtherCAT, or Ethernet for Control Automation Technology, is a high-performance network protocol designed for real-time control. I was fascinated to learn how it enables communication between devices in an automation system. The efficiency of EtherCAT allows multiple devices to communicate over a single network, reducing wiring complexity while enhancing performance.
Stepper Motor Coe Control Protocol
The CoE (CANopen over EtherCAT) control protocol is a key aspect of integrating stepper motors into EtherCAT networks. My exploration of CoE revealed its role in facilitating the configuration and control of devices. This protocol allows for the smooth exchange of data and commands, ensuring that my stepper motors operate seamlessly within the EtherCAT framework.
Key Features to Consider
When I was looking to implement stepper motors with EtherCAT, there were several key features that I made sure to evaluate:
- Compatibility: I needed to ensure that the stepper motor I was considering was compatible with EtherCAT and supported the CoE protocol. This compatibility was crucial for smooth integration.
- Performance: I paid attention to the motor’s torque and speed ratings. Depending on my application, I required a stepper motor that could deliver the necessary performance without overheating or stalling.
- Resolution and Precision: The resolution of the stepper motor directly impacts the precision of my applications. I focused on motors that offered high step counts for finer control.
- Ease of Integration: I appreciated products that came with clear documentation and support for EtherCAT configuration. This made the setup process much more straightforward.
- Feedback Mechanisms: Some stepper motors include encoders for feedback. I found that motors with feedback systems offered better performance and reliability in critical applications.
Installation Considerations
I learned that proper installation is vital for optimal performance. Here are some tips I found helpful:
- Wiring: I ensured that my wiring was organized and properly shielded to minimize interference. EtherCAT networks can be sensitive to noise, and I wanted to avoid any disruptions.
- Configuration: I spent time configuring the EtherCAT master and slaves correctly. This step is essential for ensuring that all devices communicate effectively.
- Testing: Before running my applications, I conducted thorough testing. This helped me identify any issues early on and allowed for adjustments to be made.
Applications of Stepper Motors with EtherCAT
Throughout my journey, I discovered various applications where stepper motors with EtherCAT excel. From robotics to CNC machinery, the precision and control offered by this combination are unmatched. I also found them useful in automated assembly lines and 3D printing, where accuracy is paramount.
Final Thoughts
my experience with stepper motors and EtherCAT has been enlightening. I learned that understanding the CoE control protocol and considering key features significantly impacts the effectiveness of my projects. By carefully evaluating my options and taking the time to integrate everything properly, I was able to achieve the precise control I needed for my applications.
Author Profile
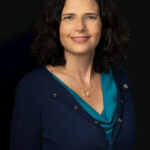
-
Hi, I’m Sarah Kroger the creator and voice behind Petite Fete Blog. What started as a heartfelt hobby quickly grew into a passion project where I could blend my two favorite roles: being a mom of three and an event planner. Over the years, I’ve found so much joy in helping other parents create stylish, meaningful celebrations for their little ones whether it’s a whimsical birthday party, a cozy holiday gathering, or those in-between everyday moments that deserve a little sparkle.
Starting in 2025, I expanded Petite Fete Blog beyond party planning. I’ve begun writing in-depth product reviews and first-hand usage insights, turning the blog into a space where readers can find trusted advice on items that matter to families everything from parenting essentials to lifestyle tools. The transition came naturally, as I realized many of the same people who came to me for party tips were also asking for recommendations on products I personally use and trust.
Latest entries
- May 5, 2025Personal RecommendationsWhy I Switched to a 4 Oz Shot Glass: My Personal Experience and Expert Insights
- May 5, 2025Personal RecommendationsUnlocking the Benefits of Dietworks Apple Cider Vinegar: My Personal Journey to Wellness
- May 5, 2025Personal RecommendationsWhy I Can’t Stop Streaming Repo! The Genetic Opera: A First-Person Journey Through This Cult Classic
- May 5, 2025Personal RecommendationsWhy I Switched to Micro USB Cords for My PS4: A Gamer’s Expert Experience